Spray Systems
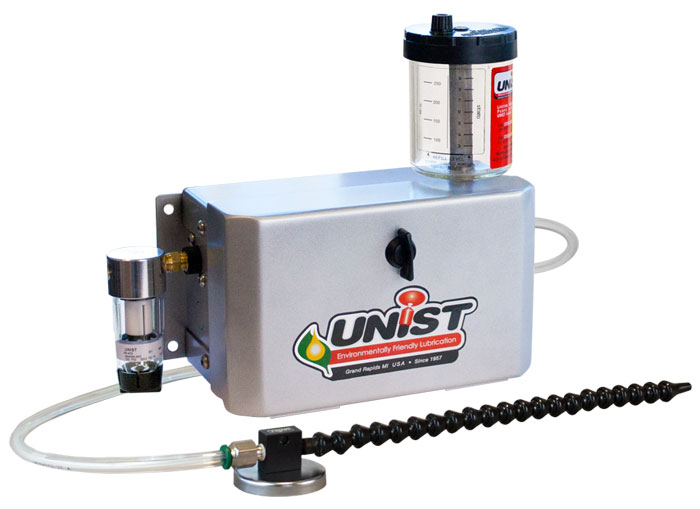
Cutting fluids can be applied (sprayed) to the machining process in a number of different ways. The most common is flood application, where a large volume of fluid is pumped to the metal removal tool contact area. The fluid is collected and then reused many times. Another method, Micro-lubrication, provides fluid to the cutting area in the form of a mist, providing the lubrication effect.
While flooding uses more fluid than misting it often serves two purposes - cooling and debris removal, but it must be collected and filtered before it can be reused. Misting, on the other hand, because of the small volume used, the fluid is not collected for reuse AND due to the low flow rates it cannot carry metal debris away as well, meaning alternative methods for debris removal must be implemented.
One of the primary driving forces behind the implementation of micro-lubrication is waste reduction. The fluid is atomized, often with compressed air, and delivered to the cutting area through a number of nozzles. Mist application of cutting fluid in only a minute amounts, typically a flow rate of 50 to 500 ml/hr which is about three to four orders of magnitude lower than the amount commonly used in flood cooling conditions, where for example, up to 10 liters of fluid can be dispensed per minute.
In stamping applications, the Uni-Roller is the best alternative to apply the most efficient amount of fluid on the stock. If the roller (see roller system) is not able to be used for some reason, a precision spray system like the Unist LV (Low Volume) system can reduce fluid significantly compared to typical airless spray systems. By introducing air to the mix, the LV nozzle spreads the fluid out more efficiently and applies less to the same area. This spray method can save 25% to 50% in fluid usage compared to airless spray systems.
In machining applications, the Unist MQL systems we provide can eliminate coolant by applying a small amount of a very rich vegetable oil onto the cutting tool, which improves tool life and finishes while it dries up the work area.